EVモーターリサイクルの効率的なスキームを
構築し、循環型社会の推進に貢献
マテリアル事業本部 栃木営業所
常次 和裕
- #カーボンニュートラル
- #環境
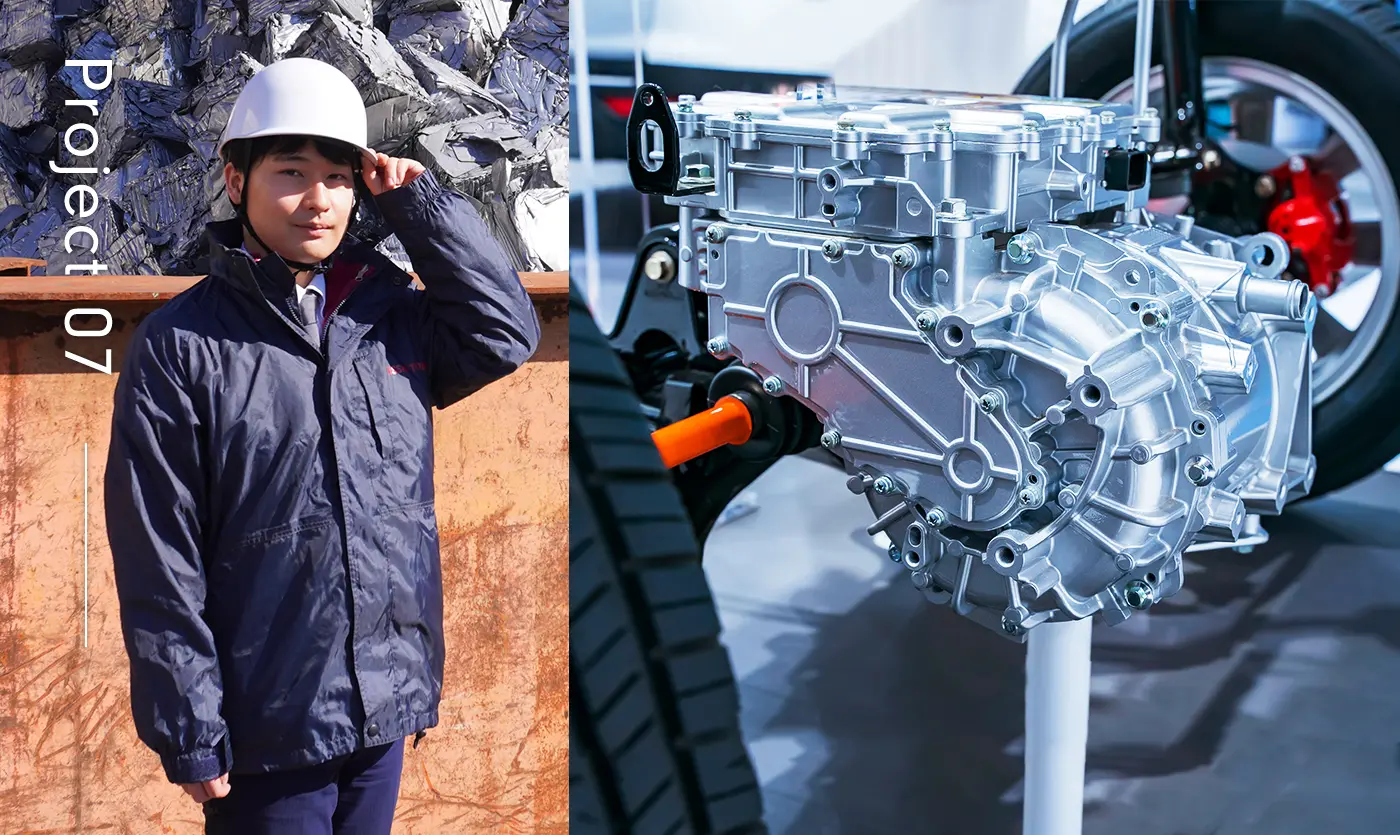
EVリサイクルのノウハウを、日産自動車栃木工場へ
日産自動車では、2007年から自動車の製造工程で発生する鉄端材(鉄スクラップ)などを資源としてリサイクルし、再び自動車製造に使用したり、外部に売却したりする取り組みを進めています。日産トレーディング(NITCO)では、このリサイクルスキームの一元管理を行っており、私は現在マテリアル事業本部の一員としてこの業務を遂行しています。
日産自動車は、時代に先駆けてEVの開発・生産を進めており、この分野においては自動車業界トップクラスの技術力、生産力を持っています。現在、環境意識の高まりとともにガソリン車からEVへのシフトチェンジが加速し、生産台数が右肩上がりで伸びる中、今後はNITCOが請け負っているような、リサイクルの推進が大きな課題となってきます。しかし、自動車業界全体として見たときに、EVリサイクルのためのスキームや技術が完全に確立されている、とはなかなか言えないのが現状です。
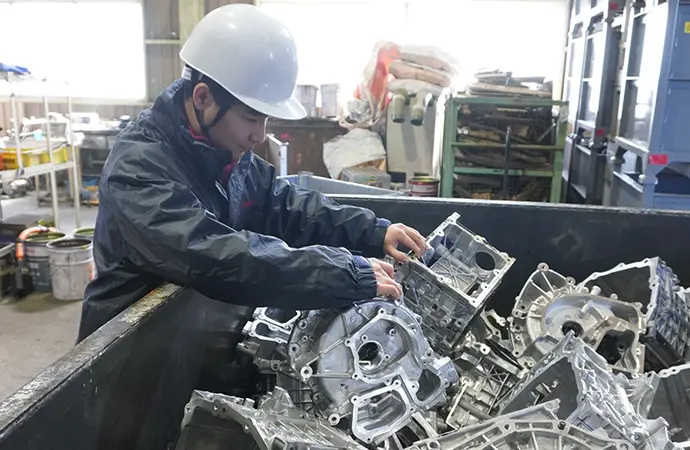
このような状況の中、既に横浜工場ではEVモーターの製造工程で生じる銅や鉄、アルミなどをリサイクル資源として活用する取り組みが進められており、そのスキーム構築や運用をNITCOが担ってきました。
2021年には、栃木工場でもEV「ARIYA」が生産されることになり、新たな製造ラインが整備されました。私は栃木工場でのEVモーターリサイクル事業もNITCOが介入できるよう、早い段階から情報収集を行い、リサイクル方法の検討や業者選定、運用の検証を積み重ね、日産グループとしてのメリットを最大化するスキームを構築、提案しました。その結果、NITCOが横浜工場同様に、栃木工場の運用を担うこととなりました。
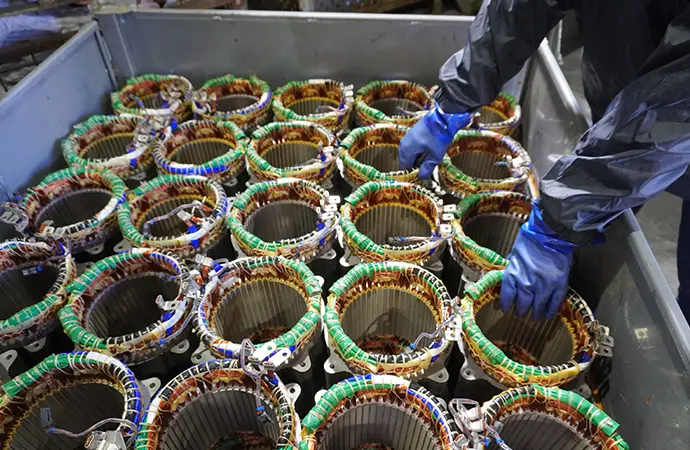

サンプル品を拠り所に、効率的な解体・分別方法の検証を重ねる
リサイクルのスキームをつくるには、まずはリサイクルに使えるモーターの端材がどのような状態で排出されるのかを知る必要があります。モーターと一口に言っても、磁力の有無や、半製品(販売品と遜色ない状態であるものの、企業としては「製造途中」と見なしている製品)と完成品の違い、素材の違いなどによって解体方法が異なってきます。幸い、栃木工場の担当者との連携は早々に行うことができたため、早い段階で「ARIYA」のサンプル品を入手し、どのような材料が、どのように分別されて出てくるのかを知ることができました。
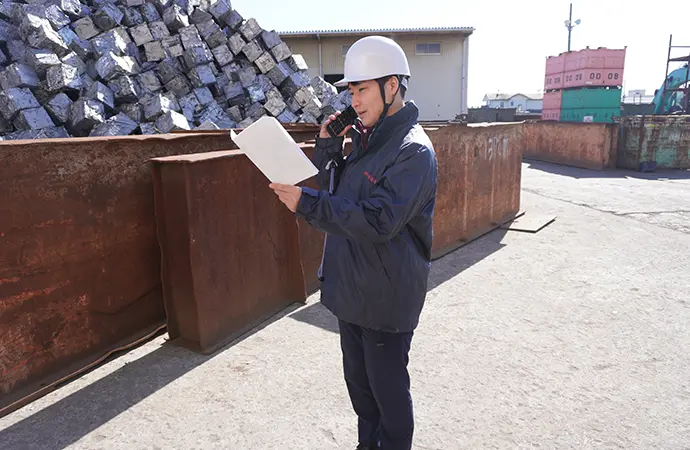
続いて、そのモーターをどうやって解体するのがベストなのかを検討しました。モーターのリサイクル全般については、横浜工場の解体現場を見学し、さまざまなアドバイスを受けました。とはいえ、栃木工場で生産するモーターは、横浜で生産されているものとは異なるため、解体・分別の方法は、新たに検討し直す必要がありました。
現在、日本にはモーターの解体を専門にしている業者はありません。ましてや新製品モーターの解体となると、どの業者にとっても未知の領域のため、NITCOとしても手探りで試行錯誤を重ねる必要がありました。そこで、栃木工場周辺のスクラップ関連企業の方々らに相談して機密保持契約を締結し、サンプルを解体してもらいました。その上で、それぞれの材料をどのように活用するかを検討していったのです。
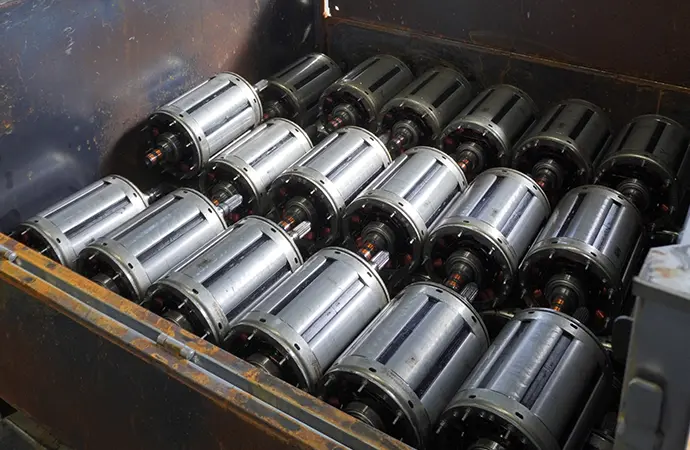
コスト削減を通じ、リサイクル事業の経済性を高める
リサイクルが環境のための取り組みであることは大前提。しかし事業でもある以上、採算が取れなければ継続は不可能です。そこでコストを抑え、いかにビジネスとして成立させるかも、検討する必要がありました。日産自動車にとって分別の負担が大きくならない範囲で、いかに引き取り量を多くし、売却益を大きくするか、メリットを最大化することを意識し、リサイクルスキーム構築に取り掛かる必要がありました。
同時に、この取り組みに協力いただく解体事業者にとってもまた、負担が少なく経済的なメリットがあるスキームにする必要がありました。できるだけ少ない工数で解体するにはどうすればいいのか、私もアイデアを出しつつ、二人三脚で検討を重ねていくこととなりました。
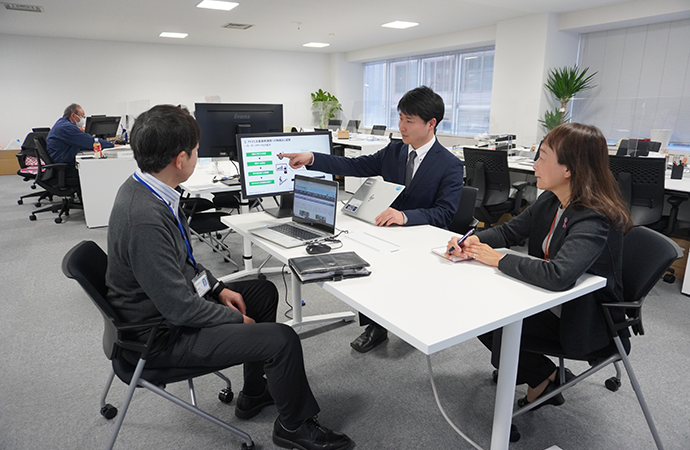
特に銅の抽出作業は、コスト削減に奮闘した代表例だと思っています。モーターを回転させる磁石の部分は、ワニスと呼ばれる接着剤で銅線がしっかりと固定されていて、簡単には解体できません。どうすれば効率よく銅を取り出せるのか、さまざまに検討する過程で、解体事業者とも議論を重ね、「工業炉の予熱でワニスを溶かす」という方法があることにたどり着きました。ゼロからワニスを溶かすよりエネルギーコストを大幅に削減でき、経済性を高められると考えたのです。
このように、試行錯誤を重ねてモーターから取り出した銅や鉄、アルミなどは再度、自動車部品として生まれ変わっています。このように大切な資源をいかに無駄なく、有効に活用できるかを考えながら進めてきました。
商社のネットワークとリサイクル事業のノウハウで、サーキュラー・コマースの実現を
日産自動車、物流会社、解体業者、NITCOの先輩方など多くの方々の協力により、栃木工場のリサイクルスキームは無事、運用開始にこぎつけることができました。栃木工場の担当者からは「早い段階から動いてくれたおかげで生産に影響を与えることなく、スムーズにリサイクル処理が行えている」と喜んでいただいています。
NITCOは日産自動車の製造に関わる部品や材料など、グローバルな輸出入を担うこの分野のプロフェッショナルです。さまざまな金属素材を扱う業者とも太いパイプを持っています。今後もその強みを生かし、さらに効率よく資源を有効活用できる方法を模索していきます。また今後、予測されるARIYAをはじめとするEVの生産増加に対応できるように、キャパシティの増強にも取り組んでいく予定です。
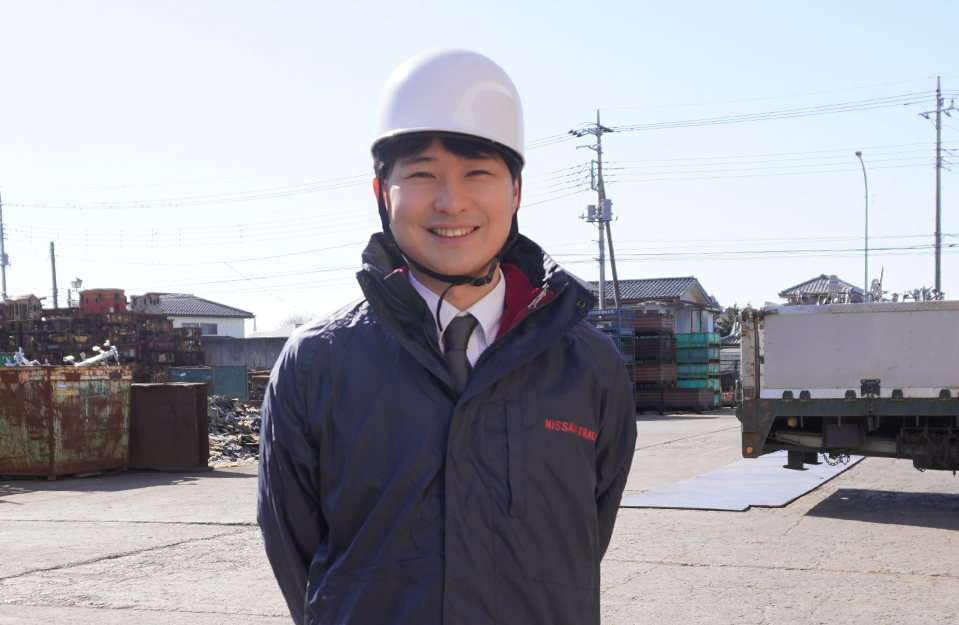
商社であるNITCOは、そのネットワークや交渉力を駆使し、効率的でコストを抑えたリサイクルスキームを構築し、ビジネスとして成立させることをミッションとしています。今後は日産グループ内のリサイクルに留まらず、日本全体で輸入に頼らずとも国内のスクラップを原料に鉄をつくることができる、そんなサーキュラー・コマース実現の一翼を担えれば嬉しいです。
関連する事業
マテリアル事業
日産自動車及びアライアンスグループである三菱自動車、ルノーの国内・海外工場及び部品メーカー向け鉄鋼製品、原料・非鉄金属、化学品等 の自動車用材料供給、情報管理及び材料のリサイクルや電力販売などの環境関連事業を通じてアライアンスグループの競争力向上及びカーボンニュートラルの実現に向けて貢献しています。
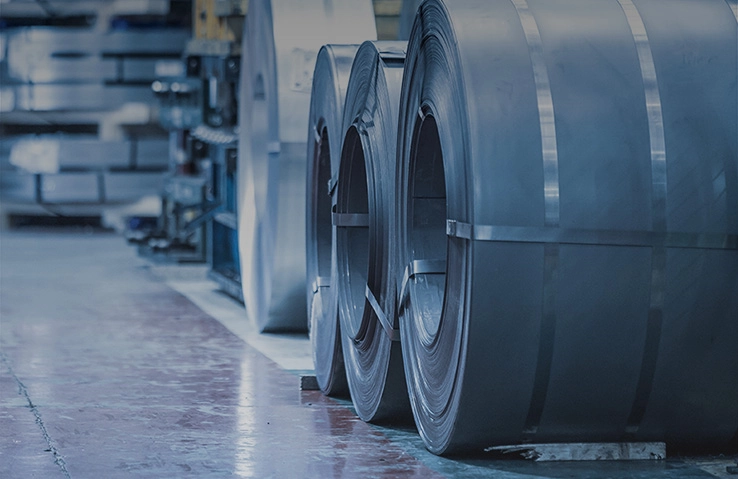